The welding industry is a major economic player. But it’s been facing inefficiencies and a chronic shortage in skilled labor. As a result, players in this sector are turning to automated welding solutions. This mainly involves the use of welding robots and AI.
How would this impact your welding company? Is AI really a threat to traditional welding jobs? What does this mean for current welders and those who wish to pursue a career in welding?
Automation has been transforming the nature of the welding workforce. Radical advances in robotics and AI are enabling machines to match, and in some cases, outperform human operators. Therefore, welding can be automated. But, robots can never truly replace human input. Instead, they augment a welder’s presence- performing tasks that would otherwise be too risky for a welder/fabricator.
In this post, I’ll explain what welding automation means and how this could affect the industry.
Can We Automate Welding Operations?
Yes, it’s possible to automate some of the tasks that welders do.
Does this mean that automation technology could displace welding jobs in the future? or AI (Artificial Intelligence) will replace welders in the near future?
No, this is not what it means.
The truth is, automated welding can never fully replace human input. For one, a robot can only do very specific tasks. So if the welding job varies even slightly, it’s not able to keep up. A welder has to reprogram it for the new task.
Also, robotic welding systems can only operate independently to a certain extent. If something goes wrong, a human operator has to intervene. Not only do they have to figure out what the problem is but also reprogram the robots.
Besides, automation is not suited for all welding applications. It’s mainly beneficial in welding tasks that call for repeatability. Thus, you can always hire welders for the non-repetitive functions.
So will this result in welding jobs replaced by robots?
Probably not.
Using robotics in welding will certainly have a negative impact on the human labor force. But, all these examples prove that manual welding has its place. Even though automating welding has benefits, there are areas where it falls short.
Most of us started with good old fashioned stick welding. Even I made mistakes like sticking the rod to the workpiece all the time and learned how to overcome those issues by practice. This is not something robots can do. Mastering in an area is where humans can do really well. This means welding jobs will always be in demand, even in the future.
What is Automation in Welding?
Robotic welding differs significantly from manual welding. The latter involves manipulating the torch or electrode holder by hand. This means an individual performs and maintains continuous control of the welding process.
Automatic welding involves robotic systems operating on their own to perform a part of the entire welding process.
There are two main types of welding automation:
- Semi-automatic
- Fully automatic
In semi-automatic, a welder/fabricator places parts into the welding fixture. The robotic system then executes the welding function. Once the weld is complete, the welder removes the finished assembly.
Semi-automatic welding involves robots working safely, but close to human operators.
In the case of fully automatic welding, a series of custom machines perform the whole welding process. From loading workpieces to manipulating the torch and performing the weld. In fact, these types of machinery are also designed to assess the quality of the final assembly.
Factors to Consider Before Moving to Automated Welding
As I have explained later in the article, switching to automated welding has its benefits. But you should keep in mind that it comes with its own challenges.
So before you decide to let go of your welders, weigh the pros of making such a move against potential cons. Here are some things to take into account:
Supply vs. Demand
A key benefit of using automatic welding machines is a boost in your production rate. This is good news if you’ve been looking to cut down on your production time.
But if you’re comfortable with your current pace, it’s wise to first assess the outcome of a supply increase. Do your clients need a drastic increase in production volume? Would they appreciate improvements in the quality and precision of welds? Would they be willing to pay more for the assembled parts?
Can Your Plant Accommodate Automatic Welding Machines?
When thinking about robotic welding machines, consider the amount of floor space available.
Some welding robots are pretty compact. But others take up a significant amount of space. Don’t forget to account for hardware space. Items like consumable dispensing systems will need more space. Essentially, if you’re limited on space, you’ll have to look for a bigger space first.
Technical Expertise Counts
The American Welding Society (AWS) projects that the shortage of skilled welding operators will reach 400,000 by 2024. There’s a high number of retiring welders. Unfortunately, younger welders aren’t replacing them fast enough.
The shortage of skilled welders presents a challenge in automated welding. The reason for this is that welding robots are best operated by experienced welders.
Such a professional can check the welding process and spot problems when they occur. But, recruiting and training experienced personnel can cost you a lot-not to mention it requires time.
Justifying the Expense
Robotic welding machines don’t come cheap. RobotWorx estimates that the average price of a robot arm is $28,000. But, the cost of a complete pre-engineered work cell starts at $50,000. Factor in the cost of training your welders and you have a very expensive project on your hands.
On the plus side, you’ll make significant savings in production costs and time. Still, it will take a while to realize a return on your investment.
So you should first assess your payback (time and production savings). Estimate the volume of parts the robot will make within a year. Compare this value to the upfront cost you’ll incur and the reductions in labor costs.
If the investment project does not have any gains, then you should reconsider your decision. Perhaps, you’d make more profit if you stick to manual welding.
When to Consider Automated Welding
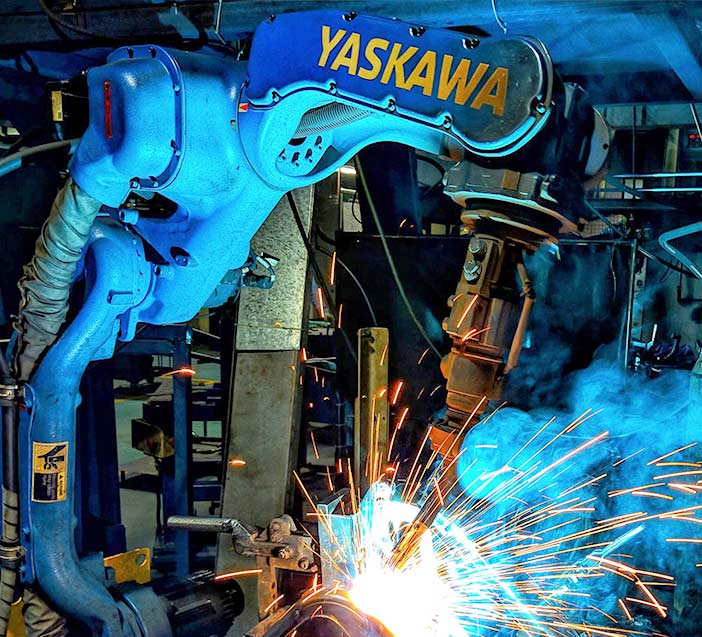
Welding tasks that call for optimal consistency
One of the advantages of an automatic welding machine is consistency. You can position the welding torch, the same way in each cycle. Similarly, this welding system will maintain the same arc length, each time.
Unfortunately, this is not the case with manual welding. Often, a welder’s level of focus wanes over time. The more hours they work on a repetitive task, the higher the likelihood of making an error.
Need to increase output
The primary reason why welding companies prefer automation is because of productivity increase.
A robotic welding machine can perform the same task as a human operator but do it 3 to 5 times faster. Contrary to a welder, these custom machines can operate continuously for days. This results in a significant increase in output.
Looking to improve the quality of the weld
Another advantage of a robotic welding machine is that it improves the quality of the weld. It maintains the perfect welding angle and velocity. It also maintains an optimal distance with a precision of about 0.04mm.
This ensures the production of each welding joint to the highest quality possible. So unlike with manual welding, you’ll never have to worry about reworking the welds.
Want to increase welders’ safety
Welders and fabricators are exposed to a multitude of risks. These include electric shock, exposure to toxic gases and flash burns. By replacing a human operator with a robotic machine, you’re reducing such risk factors.
Important to note though is that industrial accidents can still happen. This is particularly so when you have incompetent personnel handling complex automated systems. But, they don’t happen as often as when firms rely solely on manual operations.
Therefore, we can see why applying automation is profitable for a company in the long-run considering all these situations.
Disadvantages of Robotic Welding
Do you worry that robots are taking over welding jobs? Well, you don’t have to. As you’ll see below, robotic welding has major flaws. This is why experts recommend using them alongside welders who have ample experience. Here are some of the challenges of using automation in welding:
Pricey
As I mentioned earlier, a welding robot requires a significant investment. Sure, you’ll save money in the long-term. But in the short-term, you’ll need enough funds to buy and maintain your welding robot.
Rigidity
Robotic welding machines excel at doing repetitive tasks. But they fall short when it comes to flexibility.
If you’d like your welder to do a certain task differently, all you need to do is ask them to. But it’s not all plain and simple when it comes to robotic welding. You have to reconfigure the entire system. And this is assuming that you or your welders know how to reprogram it.
Risky
Relying on a completely automatic welding process is also risky. Imagine this: you decide to replace your team of welders with a fully automatic robotic system. If this robot malfunctions, you’ll have to halt your production process.
Plus, you’ll need to hire a skilled technician to fix the custom machine. And there’s no telling how long your welding robot will be down.
By comparison, it’s easier to replace a human operator. If one of your welders is ill, recruit another; no need to stop your entire production process.
The Durability of Welding Robots
In an ideal world, welding robots would never malfunction. Sadly, this is not reality. Like any other equipment, automatic welding systems aren’t exempt from defects.
The durability of welding parts- nozzles, diffusers, and liners- relies on two things. One, the item that you plan to weld and two, the welding parameters. For instance, tasks that use high amperage are tougher on welding robots.
In a nutshell, even welding robots have a lifespan. If they don’t last long, this could translate to one of the worst investments you’ve ever made.
Wrap Up
Automating welding has several benefits. It increases the precision of a weld, enhances a welder’s safety and boosts productivity.
These perks make automation a preferred alternative to manual welding. But, there are a few factors you should consider before switching to robotic welding.
These include cost, floor space, and potential market. You should also consider hiring experienced personnel. This way, you have the assurance that they can operate welding robots properly.
Related Questions
How does a welding robot operate?
Well, this machine relies on several components to create a weld. Two of the most essential parts are a wire feeder and a torch.
The movement of the robot prompts the wire feeder to send a wire filler. The torch then generates heat, which melts the released wire. The melting of this metal is what creates a weld, attaching two pieces together.
What are the applications of robotic welding?
The main applications of welding robots are resistance spot welding and arc welding:
Robotic spot welding
Spot welding is the technique of joining thin work pieces at a single point. It’s widely applied in the automobile, aerospace and packing industries.
It will be wonderful for everyone. Thank you for Amazing info.